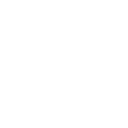
Crown Eco Reviews Waste equals energy: The biomass equation | JIGSY
The Sustainable Australia Report 2013 advises that global
trends such as population growth and growth of the middle class in Asia will
place increasing demands on energy, water and food systems. In Australia one
such impact, caused by population growth within its major cities, is the
increased cost of waste landfill as sites reach capacity limits.
Biomass waste-to-energy systems help address this issue by reducing both landfill and reliance on fossil fuels.
What is biomass?
Fossil fuels are formed from biomass and while both can produce energy, biomass is sourced from the atmosphere as part of the planet’s balanced carbon cycle, and can be therefore considered “carbon neutral”.
Biomass is organic matter including forest and mill residues, agricultural crops and wastes, wood and wood wastes, animal wastes, livestock operation residues, fast growing trees and plants, industrial and some municipal wastes such as construction and demolition wastes. Biomass is the only renewable energy source that can provide on-demand energy, heat and electricity, as well as carbon-based fuels.
Selecting the right biomass energy system
There are several processing technologies to convert biomass into energy, each with specific application depending on the biomass resource. These are typically thermal (direct combustion, pyrolysis, gasification), or biological (anaerobic, fermentation) processes. | Environmental news…
Since thermal processes are the most flexible, as they can process all forms of biomass, and the majority of proven commercial applications for heat and power utilise direct combustion and gasification technologies, this article will focus on these two technologies
Fuel supply | Most projects only consider the biomass fuels that are readily available at the time they are initiated. However, after five years, many plants operate with a very different fuel mix to that for which the plant was originally designed. It is therefore important to select a technology that allows for changes in fuel composition, for example, different energy value, moisture content, density and size. Also, the chosen technology should have the ability to accept fuels in liquid or gaseous form.
Environmental / Permit issues | Public opinion can have a significant influence on the ease or difficulty that a project experiences during the planning and permitting stages. To avoid potential difficulties, the technology should be demonstrably the best available to minimise emissions and environmental impacts.
The technology supplier | It is important to question both the maturity of the technology and the experience of the supplier. Is the technology innovative yet commercially proven? Is it out-dated? Or is it a research and development project in disguise? Is the supplier a recent start-up or an established company with many references to its name? What about the financial strength of the supplier? And finally, will the project investors and lenders support the project based on the selected technology supplier?
Thermal biomass systems
A thermal biomass energy system is comprised primarily of a fuel handling system and a biomass boiler system.
Fuel receiving and handling system | The fuel receiving and handling system can be very simple or highly automated, depending on the fuel and the plant operating philosophy. It will normally include weighing, unloading, screening, storage, reclaiming and transfer systems and should be designed to ensure reliable, consistent fuel supply to the biomass boiler.
Biomass boiler system | There are a number of biomass boiler technologies that convert biomass to steam or energy, however, for this article, we will consider only mature commercialised technologies. These are suspension fired boilers, grate boilers and fluidised bed boilers.
1. Suspension fired boilers | Suspension fired boilers consist of a horizontally mounted tube, or combustion chamber, with an open end. A fan blows combustion air into the boiler, and fuel is introduced from the side with high velocity air. Combustion is promoted when fuel and air mix as they swirl through the combustion chamber. Hot gases exit at the open end. The suspension fired boiler normally has the lowest capital cost, however it has limitations. Fuel needs to be sized to ≈5mm or less and must have less than 15% moisture (wet basis). The burner typically operates above 1250oC, and this causes thermal NOx to be formed. In addition, a percentage of the nitrogen contained in the fuel is converted to NOx during combustion. The NOx generated can be partly alleviated by selective non-catalytic reduction (SNCR) but the effectiveness of this treatment is limited because of the short reaction time available due to the boiler design.
2. Grate or stoker boilers | Grate boilers are available in many forms including slotted, pinhole, shaker and traveling. The grate supports a bed of fuel that allows air to pass up through the bed. The bed typically contains up to 45 minutes of fuel inventory; a feature that limits the boiler’s ability to adjust quickly to load changes or variations in the fuel composition heating value. The fixed grate spacing restricts the ability to switch fuels, (for example wood chips to sawdust). Moisture must be kept quite constant, and since the burner operates above 1200oC, thermal NOx is an issue, as per the suspension type boilers.
3. Fluidised bed boilers | Fluidised bed boiler technology can be used in thermal oxidation and gasification operations, and has the advantage of inherently lower emissions and greater fuel flexibility. The fluidised bed comprises a layer of sand-like material that is suspended by an upward flowing stream of air. When the air velocity is sufficient to lift the sand particles and keep them in suspension, the bed resembles a violently boiling pot of water, hence the term “fluidised bed”. The turbulence in the bubbling bed acts to efficiently spread the fuel as it is fed to the boiler and the sand particles act to abrade the fuel as it is oxidised to expose fresh fuel to the combustion process. These systems are flexible because they can accept a wide variety of fuels (singly or blended) through the same plant even with varying moistures (5%-55%) and high ash contents (55%). Fluidised bed systems typically have stable operating characteristics because the turbulent nature of the operation results in even distribution of temperature and oxygen. Fluidised bed thermal oxidation and gasification processes will be described here.
Customer support service by UserEcho