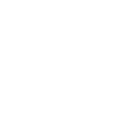
Thermal Triumphs
source: http://biomassmagazine.com/articles/9526/thermal-triumphs/
Using fast pyrolysis—gasification’s cooler, oxygenless cousin—to economically produce a bio-oil that serves as a replacement for alternative fuel oil has been a challenging endeavor. Despite its unusual properties and typically high capital and operating expenditures, however, there is increased interest around bio-oil production and utilization, and researchers and companies are achieving success in solving commercialization barriers.
One of those companies is Metso, whose technology partner, VTTTechnical Research Centre of Finland, has been working on bio-oil since 1982. Jussi Mantyniemi, general manager of technology for Metso’s power business line, says the patented, integrated bio-oil production process has three main parts, the first of which is fuel handling. This includes fuel receiving, drying of the biomass to 10 percent moisture, crushing and conveying.
Prepared fuel then enters a fluidized pyrolysis reactor where the dried biomass is pyrolysed in oxygen-free conditions. “The heat for the reaction is provided by the hot sand from the host boiler,” Mantyniemi explains. “After the reactor, in the cyclones, vapors are separated from the sand and char, which are returned to the boiler.”
Vapors from the reactor are condensed to form bio-oil, and noncondensable gases are introduced to the boiler for heat and power generation.
The technology has been thoroughly tested in a process demonstration unit at VTT, as well as a 7-ton-per-day scale unit at Metso’s research and development facility in Tampere, Finland. Metso and VTT will reach a milestone this fall, with the completion of a commercial-scale production facility in Joensuu, Finland, at a facility owned by energy company Fortum. “The pyrolysis plant is integrated into the existing CHP (combined-heat-and-power) plant, and will produce 50,000 tons annually of bio-oil,” Manthyniemi says.
Previously, for proof of concept, around 40 metric tons of bio-oil was combusted in Fortum’s 1.5 MW district heating plant in Masala, Finland.
Commissioning of the plant is scheduled for this fall. Though it may serve as proof that bio-oil can be produced and used at commercial scales, there are still hurdles to robust market development.
Market Development
According to Mantyniemi and VTT reseachers, the biggest challenge in commercialization of fast pyrolysis technology is to make bio-oil production competitive in combustion applications. In other words, the whole value chain from the fuel procurement to the end use must be capable of operating in the margin between the price of the reference fuel and the price of the feedstock. The margin for heavy fuel oil replacement is relatively small, which makes developing commercial cases very vulnerable. Cases where replacement of light fuel oil is possible are more lucrative, due to the bigger margin.
In case of Joensuu, Fortum is planning on utilizing the produced bio-oil in district heating boilers around the Joensuu and Helsinki areas for peak loads, rather than heavy and light fuel oils.
Another hurdle to commercialization is burner technology development, as relatively few burner manufacturers have developed commercially available burner models for fast pyrolysis bio-oils, and designs are sensitive to the changes in the quality of the bio-oil. This may cause problems in ignition, flame detection and flame stabilization.
On potential users of bio-oil, Mantyniemi says the main customer segments are the pulp and paper industry and heat and power plant owners who have access to biomass. “The integration of the pyrolysis plant energy flows, and utilizing the existing infrastructure, are advantages.”
Initial use of bio-oil will be replacement of heavy fuel oil in any current application like industrial boilers, district heating boilers and industrial lime kilns, he adds. “[Bio-oil’s] high-energy density, i.e. transportation cost, is low compared to other forms of bioenergy, and it can be used as a substitute to heavy fuel oil with very limited modifications to the existing equipment and process.”
Metso is on track to achieve successes in fast pyrolysis similar to what it has experienced commercializing its gasification technology, which it has spent over 30 years perfecting. According to Bill Partanen, gasification business development manager, the company’s circulating fluidized bed (CFB) gasification systems are based on many years of Cymic CFB and Hybex bubbling fluidized bed system technologies, with over 200 facilities operating worldwide.
Gasification Successes
The first CFB gasification system was installed by Gotaverken—now Metso—at a papermill in Varo, Sweden, in 1987, and is it still in operation at the mill, Partanen says. Nine years later, the power boiler business of Götaverken and Finnish boiler company Tampella were merged by Kvaerner, which was acquired by Metso in 2007. “The continued growth and development of boilers and gasification with these companies has spanned more than 30 years,” Partanen says.
As a result of lessons learned over the past 30 years, Metso currently has the two largest CFB gasification plants in successful operation in the world. The Vaasa, Finland, facility, cofires up to 40 percent forest residue in an existing 230 MW electric and 170 MW thermal pulverized coal utility boiler and is the first utility-scale application for Metso. Generating 230 MW electricity and 170 MW thermal, the facility has been in successful operation since December 2012.
There are benefits to gasification cofiring, Partanen says, one of which is reusing the existing infrastructure inclusive of the boiler/turbine, an investment cost of approximately 30 percent of a new biomass plant. Additionally, cofiring with biomass provides the option to keep an old, coal-fired plant in operation by reducing mercury, CO2, and SO2 emission limits that might otherwise require new emissions controls equipment.
The facility Metso completed in the city of Lahti, Finland, uses sorted municipal solid waste (MSW) to produce 90 MW of thermal energy and 50 MW of electricity for district heating. “This is Metso’s first demonstration facility using sorted MSW, and has been in successful commercial operation since December 2011,” Partanen says. “These are the first forest residue and sorted MSW gasification systems to demonstrate that gasification of these feedstocks can be successfully applied in both the industrial and utility sectors.”
Large-scale biomass gasification projects, such as the aforementioned, offer some advantages over small or medium-sized projects, the biggest of which is economies of scale. “Large-scale gasification can be utilized at large utility and industrial applications where smaller systems would not be cost effective,” Partanen says. “It’s more costly to build and operate multiple small systems than a single large system. The fact that Metso has demonstrated that up to 40 percent of the coal can be displaced with syngas in a utility boiler with no boiler de-rating is an important milestone. Smaller systems don’t make economic sense in utility applications.”
On attributes that have allowed Metso to overcome challenges associated with large-scale biomass gasification, Partanen says it has been Metso’s long history of R&D in gasification technology and persistence that has pushed the technology into commercialization. “[Gasification technologies] must go through a learning cycle, and that takes time,” he adds. “Success is also based on understanding what is required, and then building the equipment and systems that fit the need. An example is fuel properties, and the effects these properties will have during the gasification process. Tars have always been a problem with gasifiers, and understanding how to deal with these tars is critical…an understanding of fuels and how different fuel characteristics affect fluidized bed boiler operation is the key to how [Metso] has overcome the challenges associated with gasification.”
Customer support service by UserEcho