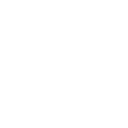
0
Westhill Consulting & Career Development: Seizing opportunities for South East Asia's oil and gas industry
http://www.freeprnow.com/pr/westhill-consulting-career-developmentseizing-opportunities
Since 2010, South-East Asia has consolidated its position as an important contributor to the global downstream market with Petronas’ recent announcement of its plan to build the new RAPID facility in Malaysia one further example of the region’s growing importance.
In reality the timing couldn’t be better - as populations across Asia continue to grow, the demand for fuel will grow exponentially, offering oil & gas operators a real opportunity to make a significant contribution to the region’s continued economic development. However, with this growing demand comes additional pressures, and with the sector still vulnerable to fluctuating oil prices, operators can ill-afford to rest on their laurels. The need to ensure their operations are as productive as possible and that cost inefficiencies are stripped out from the very outset is arguably more important than ever before.
Minimizing operational costs
When it comes to new projects oil & gas operators have traditionally been good at minimizing their CAPEX spend. However, there has been much less focus given to limiting the cost of operation of their assets. With maintenance costs typically responsible for 20-30% of the overall OPEX expenditure, this is one area where the downstream sector in South-East Asia is increasingly focusing its attention. According to some analysts the costs incurred across the globe in maintaining the next generation of oil & gas assets could equate to $0.75 trillion highlighting the scale of the prize that could be on offer here.
For a typical refinery the operational expenditure is principally dictated by three prime factors: the quantum of work carried out on the asset, the efficiency at which it can be delivered and the agreed cost rate of the resource used. In each instance there is an opportunity to significantly reduce cost outlay by focusing on a range of inter-related issues including maintenance strategies, work scheduling and the approach taken to cost & commercial management challenges.
However, it is vital that these issues are considered during the FEED (Front End Engineering Design) stage of a project for if they’re not factored in at that juncture, operators will find themselves in a situation akin to trying to catch a handful of sand. Whilst they may be able to plug some holes, the reality is that some cost inefficiencies will inevitably slip through their grips. Similarly, when it comes to the initial contracts, good intentions can quickly be forgotten as pressure to ‘get the project signed off’ sees decisions taken that result in a legacy of unnecessarily high OPEX costs for the lifetime of the asset. Given that many of these assets are in operation for over 30 years, this haste to push a project through can very easily become an expensive mistake.
Location, location, location
Another challenge facing operators when it comes to minimizing these costs is that very often their maintenance strategies are based on the Original Equipment Manufacturer’s Operations and Maintenance (OEM O&M) manuals. Whilst this ensures they comply with warranty conditions, it often overlooks two key points - the operating environment in which the refinery is located and the criticality of each asset.
In the first instance a ‘one size fits all’ approach is simply unrealistic as the operating challenges will be markedly different depending on whether the asset is located in the Arabian Gulf, the Arctic Peninsula, Jakarta Indonesia or the South China Sea. In the second case, a lack of awareness of the criticality of each asset can see operators adopt an overly expensive maintenance regime for some assets whilst at the same time under-maintain those assets whose performance is critical to the overall production levels.
The business opportunity
Those owners who focus on the key issues that affect operational costs, and who implement the right processes during both the CAPEX and OPEX phases, can significantly increase their overall productivity. Some recent examples across the globe suggest that by focusing on just 20-30% of those assets where maintenance costs are unnecessarily high, there is the potential to make savings ranging from $10-40 million per year. When considered in those terms it soon becomes clear that minimizing operational cost can have a marked impact on their business’ bottom line.
Over the past 12-18 months the downstream sector in South-East Asia has made significant steps. However, the next challenge will be to show that it can deliver sustainable improvements that will enable the region to strengthen its role as a key supplier of fuel in an ever evolving global economy. In changing times this is an opportunity the industry should not let escape from its grasp.
Westhill Consulting Career & Employment Australia found the above comments interesting.
For more information:
http://www.westhillconsulting-career.com/blog/
http://westhillconsulting-career.com/industries.html
Since 2010, South-East Asia has consolidated its position as an important contributor to the global downstream market with Petronas’ recent announcement of its plan to build the new RAPID facility in Malaysia one further example of the region’s growing importance.
In reality the timing couldn’t be better - as populations across Asia continue to grow, the demand for fuel will grow exponentially, offering oil & gas operators a real opportunity to make a significant contribution to the region’s continued economic development. However, with this growing demand comes additional pressures, and with the sector still vulnerable to fluctuating oil prices, operators can ill-afford to rest on their laurels. The need to ensure their operations are as productive as possible and that cost inefficiencies are stripped out from the very outset is arguably more important than ever before.
Minimizing operational costs
When it comes to new projects oil & gas operators have traditionally been good at minimizing their CAPEX spend. However, there has been much less focus given to limiting the cost of operation of their assets. With maintenance costs typically responsible for 20-30% of the overall OPEX expenditure, this is one area where the downstream sector in South-East Asia is increasingly focusing its attention. According to some analysts the costs incurred across the globe in maintaining the next generation of oil & gas assets could equate to $0.75 trillion highlighting the scale of the prize that could be on offer here.
For a typical refinery the operational expenditure is principally dictated by three prime factors: the quantum of work carried out on the asset, the efficiency at which it can be delivered and the agreed cost rate of the resource used. In each instance there is an opportunity to significantly reduce cost outlay by focusing on a range of inter-related issues including maintenance strategies, work scheduling and the approach taken to cost & commercial management challenges.
However, it is vital that these issues are considered during the FEED (Front End Engineering Design) stage of a project for if they’re not factored in at that juncture, operators will find themselves in a situation akin to trying to catch a handful of sand. Whilst they may be able to plug some holes, the reality is that some cost inefficiencies will inevitably slip through their grips. Similarly, when it comes to the initial contracts, good intentions can quickly be forgotten as pressure to ‘get the project signed off’ sees decisions taken that result in a legacy of unnecessarily high OPEX costs for the lifetime of the asset. Given that many of these assets are in operation for over 30 years, this haste to push a project through can very easily become an expensive mistake.
Location, location, location
Another challenge facing operators when it comes to minimizing these costs is that very often their maintenance strategies are based on the Original Equipment Manufacturer’s Operations and Maintenance (OEM O&M) manuals. Whilst this ensures they comply with warranty conditions, it often overlooks two key points - the operating environment in which the refinery is located and the criticality of each asset.
In the first instance a ‘one size fits all’ approach is simply unrealistic as the operating challenges will be markedly different depending on whether the asset is located in the Arabian Gulf, the Arctic Peninsula, Jakarta Indonesia or the South China Sea. In the second case, a lack of awareness of the criticality of each asset can see operators adopt an overly expensive maintenance regime for some assets whilst at the same time under-maintain those assets whose performance is critical to the overall production levels.
The business opportunity
Those owners who focus on the key issues that affect operational costs, and who implement the right processes during both the CAPEX and OPEX phases, can significantly increase their overall productivity. Some recent examples across the globe suggest that by focusing on just 20-30% of those assets where maintenance costs are unnecessarily high, there is the potential to make savings ranging from $10-40 million per year. When considered in those terms it soon becomes clear that minimizing operational cost can have a marked impact on their business’ bottom line.
Over the past 12-18 months the downstream sector in South-East Asia has made significant steps. However, the next challenge will be to show that it can deliver sustainable improvements that will enable the region to strengthen its role as a key supplier of fuel in an ever evolving global economy. In changing times this is an opportunity the industry should not let escape from its grasp.
Westhill Consulting Career & Employment Australia found the above comments interesting.
For more information:
http://www.westhillconsulting-career.com/blog/
http://westhillconsulting-career.com/industries.html
Сервис поддержки клиентов работает на платформе UserEcho